-
- Some services are not accessible on a smartphone.
- Sign In
- My Account
- My Cart
- Customer Service
- Bindery Parts & Equipment | Finishing Parts Equipment | Bindery Supply
- >Meech Static Control Applications for Packaging
Aerosol Packing Line
Problem:
To mitigate the fire risk, it is essential to control and monitor static charges on the film during the packaging process. Smart Control offers a solution by overseeing any ionizing system connected to the setup. Additionally, feedback sensors continuously track residual charges, automatically adjusting the ionizer's performance to neutralize detected charges. This ongoing monitoring is recorded in real-time, establishing a historical record and activating alarm alerts when issues arise.
Solution:
Controlling and monitoring the static charges on the film during the packing process ensures the risk of fire is reduced. Smart Control, provides the monitoring of any ionizing system connected, while feedback sensors monitor residual charges, automatically adjusting the ionizer's performance to compensate for charges detected. This constant monitoring is recorded in real-time, providing a history, and alarm outputs in the event of a problem.
Benefit:
The alarm alerts can be integrated with various safety measures, such as triggering the machine's emergency stop, notifying a central monitoring station, activating strobe lights, or sounding an audible alarm. This comprehensive approach ensures a secure working environment for personnel and safeguards the production process.
Bag Sealing Problems In Vertical Form Fill & Seal Machines
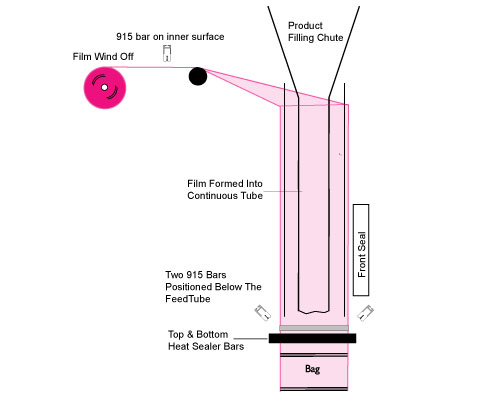
Problem:
Excessive static charges occur when unwinding packaging film, causing it to attract powders and lightweight dust from the product, especially within the seal area. This compromises sealing effectiveness and cosmetic appeal, resulting in machine downtime and product wastage.
Solution:
To address this issue, a Model 915 bar is strategically placed before the forming tube to eliminate static charges on the inner film surface. Additional 915 bars are positioned just before the sealing bar, as shown in the diagram, to neutralize any remaining static charge, preventing dust attraction and enabling proper sealing. These bar placements allow for easy removal or replacement of the filling tube without the need for demounting, ensuring efficient and hassle-free operations.
![]() |
Model 915 bar |
Cleaning External or Internal Sides Of Containers

Problem:
Traditionally, container cleaning relied on water washing systems, which came with operational costs and the need to address residual water contamination concerns.
Solution:
The Meech 957 ionizing air curtains and 261 nozzles offer an effective approach for cleaning both the exterior and interior of containers. This method ensures thorough cleaning without the expenses associated with treating and disposing of water. Another option to consider is the Meech fan-driven IonRinse, as an alternative to compressed air-driven ionizing systems.
![]() | ![]() |
957 ionizing air curtains | 261 nozzles |
Contamination and Process Issues During Blister Packing

Problem:
Friction during the unwinding of thick plastic film generates static charges, attracting contamination that can lead to permanent defects during heating and forming. Additionally, cooling plastic generates more static, causing further contamination and filling problems. The top sealing layer may also suffer from static-related issues, affecting product integrity.
Solution:
To address these challenges, it is crucial to control static charges. Contaminated rolls of material should be cleaned, with options like the Meech Non-Contact CyClean for effective removal and capture of contamination. For static control during packing, consider long-range ionizing bars like the Meech 929IPS or 971IPS to prevent product issues and contamination inclusion, ensuring quality blister packaging.
![]() | ![]() | ![]() |
Meech Non-Contact CyClean | Meech 929IPS | Meech 971IPS |
Creased Labels Or Label Alignment Issues With Self-Adhesive Labels
Problem:
Static electricity on labels, when removed from the silicone release film, causes misalignment and creases on containers.
Solution:
Utilize a Model 261v2 Flexi Nozzle with ionized airflow to neutralize label and container charges during label separation, ensuring correct placement.
![]() |
Model 261v2 Flexi Nozzle |
Powder Filling
Problem:
Static charges accumulate on the powder during delivery into the filling head, causing it to cling to the bottle's rim and repel dust onto the auger spout.
Solution:
To mitigate this problem, employ Meech's 261v2 Flexi Nozzle in conjunction with the 233v3 Pulsed DC Controller to eliminate static charges from the container. This significantly decreases the powder's attraction to the container's neck and reduces the dust repelled onto the auger spout.
![]() | ![]() |
Meech's 261v2 Flexi Nozzle | 233v3 Pulsed DC Controller |
Prototyping and Label Testing
Problem:
IML labels aim to offer high-quality graphics on finished products cost-effectively, but their materials can impact their suitability for IML applications. Any conductive properties in the label production process can reduce the adhesion strength of the label to the mold tool and allow the charge generated on the label to dissipate. Metalized plastics or conductive inks can disrupt or diminish the label's adhesion to the mold tool, leading to label slippage or incomplete attachment. Surface resistance meters can only measure the label's surface properties and cannot provide information about the material beneath the surface coating.
Solution:
The most reliable method for assessing label suitability is to charge the label while it is in contact with a grounded plate. As shown in Figure 1, a sample label is charged against an 800g aluminum sheet. In Figure 2, the aluminum sheet remains suspended solely due to the static charge applied. If the label sparks or slips during or after the charging process, it is not suitable for IML applications. This testing can be performed using a Meech B995R-IML-MAN-EXTEND & A994IML generator. This testing equipment is also suitable for:
- Batch testing label stocks to ensure their suitability for use in IML applications before adding them to the inventory for later use.
- Manual prototyping of IML products before automating production.
- Producing small batch samples for marketing purposes.
Reduced Material Overlap On Horizontal Over Wrapper
Problem:
Horizontal over wrappers apply heat shrink film around a forming tube, with the product passing through the tube in a continuous process to be enclosed within the film. The current industry standard requires a 20-30mm overlap of the film to create a seamless, continuous seal. A narrower overlap increases the risk of the film separating during the shrink process, while a wider overlap leads to unsightly wrinkles in the packaging, along with higher material costs. This problem poses an unnecessary challenge for Fast Moving Consumer Goods (FMCG) manufacturers.
Solution:
By introducing an electrostatic charge to the film overlap, it effectively locks the two surfaces together, preventing any separation issues. The electrostatic bond between the overlapping surfaces allows for a much neater seam of only 3-4mm. As the film undergoes shrinkage, the two overlap edges securely bond together, resulting in a clean, well-defined edge seam. This not only conserves a significant amount of film but also contributes to environmental sustainability and profitability. In the image, the left noodle pot's film wrap overlap is visibly wrinkled, distorting the film's surface. In contrast, the pot on the right exhibits no noticeable wrinkles in the film surface, and the overwrap is nearly imperceptible, allowing the graphic designs and marketing messages to be prominently displayed.
Stacking & Pinning Food Sachets Before Wrapping
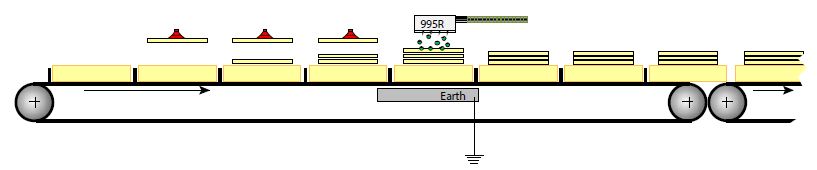
Problem:
Manufacturers of dry food products that require additional sachets or cooking instructions to be enclosed within the packaging often face issues with these sachets or literature slipping or becoming separated. Such packaging failures can result in manufacturing rejects and increased operational expenses. In this specific case involving dry noodle biscuits, sachets containing dried vegetables, oil, and flavorings are intended to remain securely in place on top of the biscuit during automated packing. Any failure at this stage could lead to customer dissatisfaction and the rejection of the product or brand by consumers.
Solution:
The application of static electricity in a scientific manner offers a prompt and effective solution to this packaging-related problem. Immediately after positioning the sachets onto the noodle biscuits, a high-voltage charge is applied to the product, causing the sachets to adhere firmly to the noodles below. This electrostatic charge will persist for a sufficient duration, preventing the sachets from slipping off the noodle biscuit. This ensures consistent and accurate packaging, ultimately leading to increased customer satisfaction and cost savings.
Static Caused By Cans On Plastic Conveyors
Problem:
A plastic conveyor belt generates electrostatic charges that can cause various problems in a production line. Metal cans moving along the conveyor tend to accumulate these static charges, leading to shocks for operators when handling the cans. Furthermore, these static discharges stored in the containers can damage the electrical circuits of the weighing scales. Plastic containers are also susceptible to static-related issues. Static discharges within the containers can trigger metal detectors, causing the product to be rejected. Additionally, inaccuracies in weight measurement may lead to product rejection due to the interference caused by static charges. Moreover, static charges can attract contaminants to the charged conveyor belt, resulting in cross-contamination and increased product rejection rates.
Solution:
To mitigate these issues, installing a Meech 929IPS Ionizing Bar over the conveyor system is recommended. This ionizing bar effectively neutralizes the static charges generated by the conveyor belt, leading to a reduction in reject rates and an overall improvement in production efficiency.
![]() |
Meech 929IPS Ionizing Bar |
Static Control During Conveying & Palletising Of Bottles
Problem:
Bottles produced by a blow molding machine carry a significant static charge as they exit the process. This static charge tends to make the bottles topple over on the conveyor or collation table, leading to blockages, product damage, and the attraction of contaminants.
Solution:
To address this issue effectively, implementing a 971 system for neutralizing the static charge on the bottles as they exit the conveyor, and also controlling residual and regenerating charges as the bottles cool on the collation table, proves to be an efficient solution. This approach maximizes production efficiency and minimizes wastage.
![]() |
971 system |
Static Control During Weighing Or Assembly Of Small Parts
Problem:
The process of weighing small parts or assembling electrical components can be negatively impacted by the presence of electrostatic charges. These electrical charges can be generated by the clothing worn by operators and transferred to the product.
Solution:
Installing a 971 Pulsed DC system above the work area effectively mitigates the issue by minimizing static charges on both operators and the product, ensuring smoother and more accurate operations.
![]() |
971 Pulsed DC system |
Ensuring Proper Label Alignment by Controlling Static in Tamper Seals and Shrink Sleeves
Problem:
Tamper sleeves and bottle sleeves often encounter issues with the sleeves not aligning correctly on the container. This can lead to the sleeve being shrunk in an incorrect position, causing problems with the packaging.
Solution:
To prevent electrostatic charges from interfering with label alignment, it's essential to neutralize the sleeve during the positioning process onto the container. Installing a 915 bar behind the label delivery head effectively neutralizes the electrostatic charges, ensuring that labels sit in the correct position during application.
![]() |
915 bar |
Static Control On A Vacuum Drum Labeller
Problem:
Label stock entering the label applicator often accumulates high levels of static charges at the leading and trailing ends of the label. This static charge buildup leads to several issues, including labels wrapping around the rotary knife. Inappropriate glue application to the vacuum drum. Labels adhering to the vacuum drum instead of the intended bottles.
Solution:
To address these problems effectively, it is crucial to neutralize the static charge on the label stock before it enters the label applicator. Installing two 915 bars in the setup before the nip roller effectively reduces the static charges, preventing misfeeding and subsequent line stoppages, as illustrated in the diagram.
![]() |
915 Bar |
Preventing Misfeeding on a Stretch Hood Palletizer through Static Control

Problem:
During the production of the layflat tube, material blockages can occur, leading to static charges being generated during the unwinding process. These issues result in excessive resistance when attempting to open the tube and remove it from the gripping fingers.
Solution:
To address this problem effectively, installing a Hyperion 924IPS Bar approximately 20mm from the web path, just before the last path roller before the nip rollers on top of the wrapper, proves to be a solution. This setup removes a significant portion of the static charge generated during unwinding and reduces some of the blockage-related charges between the layers, ensuring consistent and reliable tube opening.
![]() |
Hyperion 924IPS Bar |
Static Issues During Pallet Wrapping
Problem:
Pallet wrapping can give rise to various issues, depending on the nature of the product being wrapped. Specific concerns include:
- Risk of igniting aerosol can gases.
- Attraction and transfer of contaminants onto the product.
- Potential electrostatic discharge to operators.
Solution:
To address these challenges effectively, it's crucial to neutralize the charge on the film as it is applied to the pallet, effectively controlling charges at the final point of generation. The use of the 935 Blower provides the necessary range to operate effectively over the required distances.
Static Issues During Thermoform Tray Delivery & Waste Rewind
Problem:
The generation of static charges on thermoformed containers is increased during the cooling of the product. The stacking of the trays may lead to the containers repelling from each other and falling over. The skeleton being rewound will hold massive charges resulting in painful static shocks to operators.
Solution:
To mitigate these problems effectively, it is crucial to neutralize the static charges on the containers while they are on the collation table, allowing for stable stacking without toppling. Two options for achieving this are: Utilizing a 935 blower, which can also assist in the cooling process, or implementing a Meech 971 system. Additionally, controlling charges on the rewound skeleton can be achieved through the use of a Meech 971 system.
![]() |
Meech 971 system |
Static Pinning An Interleaf On Metal Or Glass
Problem:
When stacking finished sheet products made of materials like glass, aluminum, steel, or others, there's a significant risk of surface damage occurring. While using an interleaf can protect the surface, it also adds to the overall handling time, which can be inconvenient.
Solution:
To address this issue efficiently, automated production lines can incorporate the interleaf onto the surface of the product during the conveying process. This can be achieved through electrostatic pinning. By passing both the sheet and the interleaf over a 993R bar, a temporary bond is induced without the risk of marking or damaging the finish of the product. However, when dealing with insulative materials, it's essential to position an earth potential on the opposite side of the sheet to ensure the effectiveness of the bonding process.
![]() |
993R bar |
Static Pinning Of Loose Leaf Flyers In CD & DVD Packaging
Problem:
When closing CD/DVD jewel cases that contain marketing flyers or advertising materials, these inserts often shift out of place.
Solution:
To prevent the flyer from moving when closing the jewel case lid, an effective solution is to electrostatically secure it in place. This can be accomplished by using a single-point pinning head, which minimizes the electrostatic charge. This approach enables the jewel case to be closed smoothly while minimizing static-related issues when applying the overwrap.
Static Pinning Of Protective Laminate To Web Based Materials
Problem:
In the production of finished web materials, there may be a need to introduce a protective layer before rewinding. Additionally, when creating bags using two webs, it's essential to bond both webs together before welding and slitting.
Solution:
Electrostatic pinning offers an ideal solution in both scenarios, as it doesn't involve the use of chemical agents and can be easily removed when no longer needed, leaving no physical or chemical markings behind. Here are the recommended pinning methods:
- Utilizing a Meech 993R bar for inducing block pinning.
- Employing a 995 system for edge pinning.
- Implementing 995 single-point pinning heads for localized pinning, which is particularly effective for precise applications.
![]() | ![]() | ![]() |
Meech 993R bar | 995 system | 995 single-point pinning heads |
Static Problems With Thermal Plastic Over Wrap
Problem:
When the film unwinds and travels over various machine parts, rollers, and web guides, a significant static charge builds up. This results in the film adhering to the machine frame, rollers, or itself rather than properly conforming around the product to be wrapped.
Solution:
A 915 Ionizing Bar installed at point “A” (see diagram) will prevent the film from wrapping around the rollers. A 915 Bar should be installed at “B” (see diagram) if the film is not forming around the product properly, and is sticking to itself or the machine frame.
![]() |
915 Ionizing Bar |
Tamper Seal Issues Due To Powder Inclusion In Seal
Problem:
When packaging powders in small plastic containers using a carousel indexing system, issues can arise during the filling process:
- The powder adheres to the exterior and coats the inner walls of the container.
- Powder adheres to the filling head.
- Accumulation of powder leads to incorrect filling, and contamination of the container's exterior can result in customer rejection.
Solution:
To resolve these challenges effectively, implement the following solutions: Install two 261 Nozzles at the index position immediately before the filling station. One nozzle should be directed at the exterior of the container, while the other should target the interior. Position a model 912 Circular bar around the filling head, aligning it with the end of the dispensing tube. By adopting these measures, you can eliminate powder adhesion to the container walls and the accumulation of powder on the filling head, ensuring a more reliable and contamination-free filling process.
![]() |
261 Nozzles |
Window Patcher Film Sticking To Knife & Rollers
Problem:
Materials like cellophane used to create windows in packaging boxes and envelopes tend to generate static charges as they unwind from the roll. Additionally, the rotary knife used in the process produces high static charges at the leading and trailing ends of the film. This causes the film to adhere to the knife and rollers, resulting in machine stoppages and production loss.
Solution:
To address these challenges effectively, consider the following solution: Install a Meech 924IPS Bar over the material's web path just before it enters the knife cylinder. This installation will neutralize the static charges on the material, preventing it from sticking to the vacuum drums. One notable advantage of the 924IPS Bar is its compatibility with a 24V power supply, simplifying the installation process.
![]() | ![]() |
924IPS Bar | 24V power supply?? |
Wrapping & Contamination Problems With Bottle Overwrapper Wrap Machine
Problem:
There are three primary areas of concern when dealing with this type of packaging machine: Dust attraction during the unwinding of the web. Electrostatic attraction of the web to the cutting knife and vacuum transfer belt. Electrostatic attraction of the sheet to itself during the overwrapping process.
Solution:
To resolve these concerns effectively, the following solutions are implemented: Utilize a Meech 935 ionizing blower to manage charges on both unwinding rolls, addressing dust attraction during web unwinding. Employ a Meech 915 bar to neutralize charges on the web before it enters the sheeting knife area, mitigating electrostatic attraction to the cutting knife and vacuum transfer belt. Implement a Meech 971 bar to prevent electrostatic charges from causing sheets to be pulled out from under the containers being wrapped, thus addressing electrostatic attraction during the overwrapping process.
![]() | ![]() | ![]() |
Meech 935 ionizing blower ? | Meech 915 bar | Meech 971 bar |